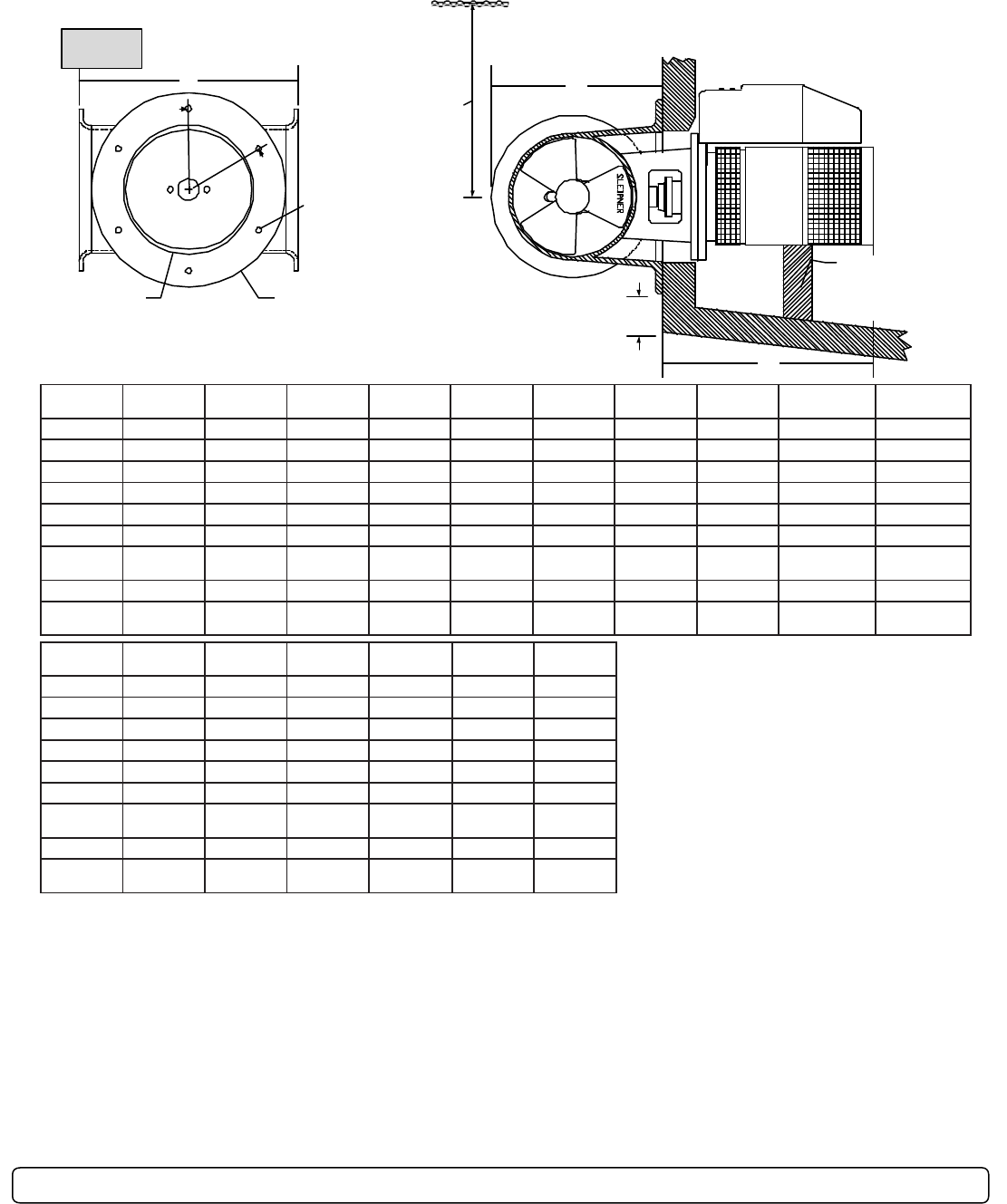
Installation
To achieve maximum effect, reliability and durability from your Sidepower Sternthruster, a correct installation is very
important.
Please follow the instructions carefully, and make sure that all checkpoints are carefully controlled.
1. Make sure that there are enough space both inside and outside the transom of the boat (see FIG 1).
Outside of flange:
E
Cut out in stern:
F
Bolt holes dia :
G
Bolt postion radius :
H
60°
D
A
PS !
Necessary
support
of motor.
Minimum is
hulls bottom
thickness
C
B
W.L.
FIG. 1
Stern thruster installation manual Version 1.6 - 2005
2
Additional considerations for positioning of stern thruster.
Make sure that the stern-tunnel does not disturb the waterflow under the hull
Ensure that when installed the thruster does not foul exisiting equipment inside the boat like steerage links etc.
It is essential that the motor is supported so that the total weight is not on the tunnel alone.
Make sure that the water flow from the thruster are not intereferred to much by sterndrives, trimtabs etc. as this
will reduce the thrust considerably.
It is possible to mount the tunnel off the boat’s centre line if necessary.
If the stern thickness is to much for the thruster in question you can easily remove material in the necessary area
to fit the thruster. The stern thickness even here will never have to be less than the max. measurement given as
max. stern thickness.
Measurements ref.
mm / inch
SP30Si / SP40Si SP55Si SP75Ti SP95Ti SP125Ti SP155TCi SP200TCi
SP200TCi-32 /
SP240TCi
SP285TCi
A 200mm / 7,87'' 225mm / 8,90" 312mm / 12,30" 349mm / 13,70" 363mm / 15,10" 386mm / 15,20" 419mm / 16,50" 440mm / 17,30" 404mm / 15,90"
B 190mm / 7,48'' 256mm / 10,08" 256mm / 10,08" 256mm / 10,08" 340mm / 13,39" 340mm / 13,39" 360mm / 14,20" 420mm / 16,54" 420mm / 16,54"
C 135mm / 5,31'' 150mm /5,91" 200mm / 7,87" 200mm / 7,87" 250mm / 9,84" 250mm / 9,84" 300mm / 11,81" 300mm / 11,81" 300mm / 11,81"
D 197mm / 7,76'' 337mm / 13,30" 337mm / 13,30" 337mm / 13,30" 350mm / 13,80" 350mm / 13,80" 350mm / 13,80" 456mm / 18,00" 456mm / 18,00"
E ø217mm / 8,54'' ø300mm / 11,80" ø300mm / 11,80" ø300mm / 11,80" ø300mm / 11,80" ø300mm / 11,80" 356mm / 14,02" ø396mm / 15,60" ø396mm / 15,60"
F ø160mm / 6,30'' ø200mm / 7,84" ø200mm / 7,84" ø200mm / 7,84" ø200mm / 7,84" ø200mm / 7,84" ø260mm / 11,24" ø265mm / 10,40" ø265mm / 10,40"
G 6 x ø6,5mm / 0,26'' 6x ø10,5mm / 0,41" 6x ø10,5mm / 0,41" 6x ø10,5mm / 0,41" 6x ø10,5mm / 0,41" 6x ø10,5mm / 0,41" 8x ø10,5mm / 0,41" 8x ø10,5mm / 0,41" 8x ø10,5mm / 0,41"
H ø98mm / 3,86'' ø129mm / 5,08" ø129mm / 5,08" ø129mm / 5,08" ø129mm / 5,08" ø129mm / 5,08" ø315mm / 12,40" ø345,6mm / 13,60" ø345,6mm / 13,60"
Max. Stern
thickness
14mm / 0,55'' 35mm / 1,38" 54mm / 2,13" 54mm / 2,13" 60mm / 2,36" 60mm / 2,36" 50mm / 1,97" 60mm / 2,36" 60mm / 2,36"
Measurements ref.
mm / inch
SP100HYD SP220HYD SP300HYD SP550HYD
A 158mm / 6,22" 178mm / 7,01" 208mm / 8,19" 259mm / 10,20"
B 256mm / 10,08" 340mm / 13,39" 420mm / 16,54" 570mm / 22,44"
C 200mm / 7,87" 300mm / 11,81" 300mm / 11,81" 380mm / 14,96"
D 337mm / 13,30" 350mm / 13,80" 456mm / 18,00" 550mm / 21,65"
E ø300mm / 11,80" ø300mm / 11,80" ø396mm / 15,60" ø600mm / 23,62"
F ø200mm / 7,84" ø200mm / 7,84" ø265mm / 10,40" ø400mm / 15,75"
G 6x ø10,5mm / 0,41" 6x ø10,5mm / 0,41" 8x ø10,5mm / 0,41" 12x ø13mm / 0,51"
H ø129mm / 5,08" ø129mm / 5,08" ø345,6mm / 13,60" ø530mm / 20,87"
Max. Stern
thickness
8
8
8
8
SE30/40 SE60 SE80 SE100 SE120 SE170 SE210
SH100 SH240 SP300HYD SH420/550
BOLT ON INSTALLATION
2a. Once the place for the installation has been decided, hold the tunnel in place in the horizontal position and
mark the bolt holes. Remove the tunnel and it is then possible to calculate and mark the centre (see Fig. 1).
3a. It is important that the tunnel flange sits flush on the transom. If this is not case, then the fitting area on the
transom will have to be worked to ensure a snug fit.
PS ! Take care with grinders as it is very easy to remove to much fibreglass
At this time, cut out the centre hole and the transom to the same internal diameter as the tunnel flange and
drill the bolt holes. Before actual fitting the stern tunnel, we recommend that the prepared area is sealed with
a gelcoat or similar to ensure there is no water ingress.
4a. Before fitting the tunnel to the transom, install the gear leg to the tunnel as described in the thruster installation
manual. We recommend that you fit the oil feed pipe also before the tunnel is bolted to the transom.
Special installation points described on page 7 of this manual.
5a. When fitting the tunnel, ensure that there is ample sealant (Sikaflex or similar) in the sealing tracks of the
tunnel flange and around the bolts to make a water tight fitting (see FIG. 2&3).
Bolts, washers and nuts are not included as they will vary depending on the transom thickness. We
recommend A4 stainless with A4 lock nuts and A4 washers of a large diameter on both outside and inside.
Bolts diameter (stainless steel):
ø 6mm or 1/4” for SP 30 Si & SP 40 Si
ø 10mm or 3/8” for SP 55 Si & SP 75 Ti & SP 95 Ti & SP 125Ti & SP 155 TCi
ø 12mm or 1/2” for SP200TCi & SP 240 TCi & SP 285 TCi
6a. The electromotor must have a solid support so that the weight
can not cause a twisting action on the tunnel (see FIG. 4).
7a. Refer to the installation manual for the recommended thruster fitting.
Stern thruster installation manual Version 1.6 - 2005
Motor support
MUST be
installed
FIG. 4
FIG. 3
SEALANT
WASHERS
LOCKNUT
OR DOUBLE
NUTS
3
FIG. 2
SEALANT
Version 1.7 - 2009
Measurements
mm/inch
SE30/40 SE60 SE80 SE100 SE120/SE150 SE130 SE170 SE210 SP200TCi-32/
SP240TCi
SP285TCi
A 200mm/7.87” 225mm/8.90” 312mm/12.30” 349mm/13.70” 407mm/16.02” 363mm/15.10” 386mm/15.20” 419mm/16.50” 440mm/17.30” 404mm/15.90”
B 190mm/7.48” 265mm/10.08” 256mm/10.08” 256mm/10.08” 300mm/11.81” 340mm/13.39” 340mm/13.39” 360mm/14.20” 420mm/16.54” 420mm/16.54”
C 135mm/5.31” 150mm/5.91” 200mm/7.87” 200mm/7.87” 215mm/7.87” 250mm/9.54” 250mm/9.54” 300mm/11.80” 300mm/11.81” 300mm/11.81”
D 197mm/7.76” 337mm/13.30” 337mm/13.30” 337mm/13.30” 330mm/13.00” 350mm/13.80” 350mm/13.80” 350mm/13.80” 456mm/18.00” 456mm/18.00”
E ø217mm/8.54” ø300mm/11.81” ø300mm/11.81” ø300mm/11.81” ø300mm/11.81” ø300mm/11.81” ø300mm/11.81” ø356mm/14.02” ø396mm/15.60” ø396mm/15.60”
F ø160mm/6.3” ø200mm/7.84” ø200mm/7.84” ø200mm/7.84” ø200mm/7.84” ø200mm/7.84” ø200mm/7.84” ø260mm/11.24” ø265mm/11.40” ø265mm/11.40”
G 6 x
ø6,5mm/0.26”
6 x
ø10,5mm/0.41”
6 x
ø10,5mm/0.41”
6 x
ø10,5mm/0.41”
6 x
ø10,5mm/0.41”
6 x
ø10,5mm/0.41”
6 x
ø10,5mm/0.41”
8 x
ø10,5mm/0.41”
8 x
ø10,5mm/0.41”
8 x
ø10,5mm/0.41”
H ø98mm/3.36” ø129mm/5.08” ø129mm/5.08” ø129mm/5.08” ø129mm/5.08” ø129mm/5.08” ø129mm/5.08” ø315mm/12.40” ø345,6/13.60” ø345,6/13.60”
Max stern
thickness
14mm/0.55” 35mm/1.38” 54mm/2.13” 54mm/2.13” 54mm/2.13” 60mm/2.36” 60mm/2.36” 50mm/1.97” 60mm/2.36” 60mm/2.36”
Measurements
mm/inch
SH100 SH160 SH240 SP300HYD SH420 SH550
A 172mm/6.72” 172mm/6.72” 191mm/7.52” 195mm/7.68” 257mm/10.12” 257mm/10.12”
B 256mm/10.08” 300mm/11.81” 340mm/13.39” 420mm/16.54” 570mm/22.44” 570mm/22.44”
C 200mm/7.87” 215mm/7.87” 300mm/11.81” 300mm/11.81” 570mm/22.44” 570mm/22.44”
D 337mm/13.30” 330mm/13.00” 350mm/13.80” 456mm/18.00” 550mm/21.65” 550mm/21.65”
E ø300mm/11.81” ø300mm/11.81” ø300mm/11.81” ø396mm/15.60” ø600mm/23.62” ø600mm/23.62”
F ø200mm/7.84” ø200mm/7.84” ø200mm/7.84” ø265mm/11.40” ø400mm/15.75” ø400mm/15.75”
G 6 x
ø10,5mm/0.41”
6 x
ø10,5mm/0.41”
6 x
ø10,5mm/0.41”
8 x
ø10,5mm/0.41”
12 x
ø13mm/0.51”
12 x
ø13mm/0.51”
H ø129mm/5.08” ø129mm/5.08” ø129mm/5.08” ø345,6mm/13.60” ø530mm/20.87” ø530mm/20.87”
Max stern
thickness
- - - - - -