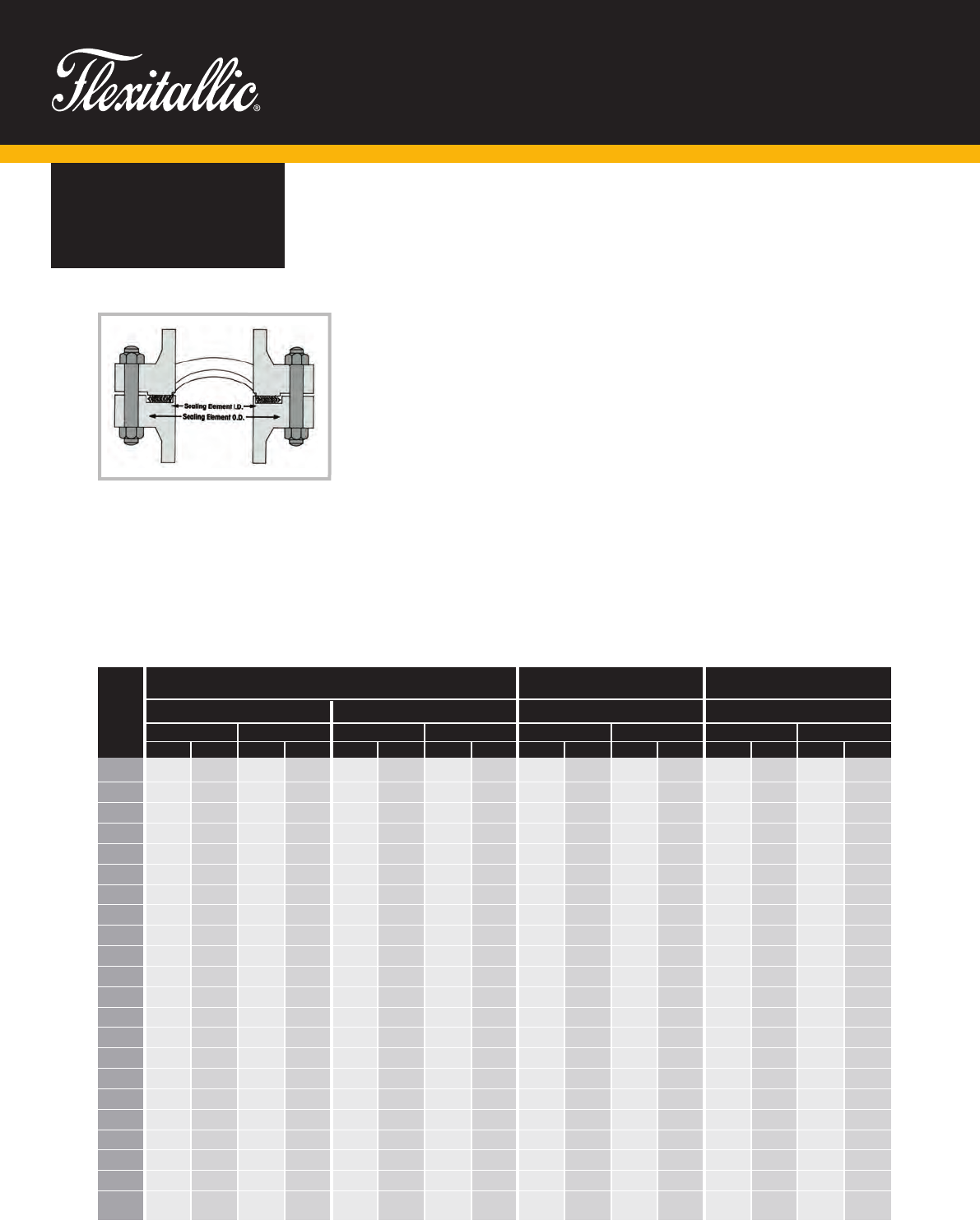
16. www.flexitallic.com
GENERAL NOTES
All dimensions are in mm amd inches.
*It is essential that Style R gaskets are fitted with a compression stop. Without a correctly dimensioned stop the gasket can easily be over-compressed resulting in failure. To provide a
compression stop the depth of the tongue, groove or recess should be controlled to provide optimum compressed gasket thickness with metal to metal contact on the flange faces.
There are three types of Style R gaskets:
(a) Style R-1 indicates gaskets for use with
large male and female flanges.*
(b) Style R-3 indicates gaskets for use with
large tongue and groove flanges.
(c) Style R-4 indicates gaskets for use with
small tongue and groove flanges.
*As a general rule, the use of Flexitallic Spiral
Wound Gaskets with small male and female
flange facings is not recommended.
Dimensional limitations established by the
proportions of the small tongue and groove
facings limit the possibility of increasing gasket
dimensions to improve the load carrying capacity
in the higher pressure series. For this reason, it is
suggested that large tongue and groove facings
be selected for new construction when class 900,
1500 and 2500 flanges are to be used.
DIMENSIONAL
DATA
STYLE R
Flexitallic dimensions for use with Male & Female and Tongue & Groove
ASME 16.5 & BS EN1092
Standard Style R gaskets embody all the
exclusive features of Flexitallic design for
keeping compression values in balance with
bolting and providing adequate resilience to
compensate for variable stresses encountered
in service. Standard Style R gaskets are
manufactured to a nominal thickness of .125"
(3.2mm). Optimum compression is in the range
of .090" to .100" (2.3mm to 2.5mm) thick.
STYLE R1 FOR LARGE MALE & FEMALE STYLE R3 FOR LARGE TONGUE & GROOVE STYLE R4 FOR SMALL TONGUE & GROOVE
NOMINAL
PIPE
SIZE
SEALING ELEMENT CLASS 150-1500 SEALING ELEMENT CLASS 2500 SEALING ELEMENT CLASS 150-2500 SEALING ELEMENT CLASS 150-2500
ID OD ID OD ID OD ID OD
¼ 0.50 12.7 1.00 25.4 ----0.50 12.7 1.00 25.4 ----
½ 1.00 25.4 1.38 34.9 0.19 20.6 1.38 34.9 1.00 25.4 1.38 34.9 1.00 25.4 1.38 35.1
¾ 1.31 33.3 1.69 42.9 1.06 27.0 1.69 42.9 1.31 33.3 1.69 42.9 1.31 33.3 1.69 42.9
1 1.50 38.1 2.00 50.8 1.25 31.8 2.00 50.8 1.50 38.1 2.00 50.8 1.50 38.1 1.88 47.8
1 ¼ 1.88 47.6 2.50 63.5 1.63 41.3 2.50 63.5 1.88 47.6 2.50 63.5 1.88 47.6 2.25 57.2
1 ½ 2.12 54.0 2.88 73.0 1.88 47.6 2.88 73.0 2.12 54.0 2.88 73.0 2.12 54.0 2.50 63.5
2 2.88 73.0 3.62 92.1 2.38 60.3 3.62 92.1 2.88 73.0 3.62 92.1 2.88 73.0 3.25 82.6
2 ½ 3.38 85.7 4.12 104.8 3.00 76.2 4.12 104.8 3.38 85.7 4.12 104.8 3.38 85.7 3.75 95.2
3 4.25 108.0 5.00 127.0 3.75 95.3 5.00 127.0 4.25 108.0 5.00 127.0 4.25 108.0 4.62 117.5
3 ½ 4.75 120.6 5.50 139.7 ----4.75 120.6 5.50 139.7 4.75 120.6 5.12 130.2
4 5.19 131.8 6.19 157.2 4.75 120.7 6.19 157.2 5.19 131.8 6.19 157.2 5.19 131.8 5.69 144.5
4 ½ 5.69 144.5 6.75 171.5 ----5.69 144.5 6.75 171.5 ----
5 6.31 160.3 7.31 185.7 5.75 146.1 7.31 185.7 6.31 160.3 7.31 185.7 6.31 160.3 6.81 173.0
6 7.50 190.5 8.50 215.9 6.75 171.5 8.50 215.9 7.50 190.5 8.50 215.9 7.50 190.5 8.00 203.2
8 9.38 238.1 10.62 269.9 8.75 222.3 10.62 269.9 9.38 238.1 10.62 269.9 9.38 238.1 10.00 254.0
10 11.25 285.8 12.75 323.9 10.75 273.1 12.75 323.9 11.25 285.8 12.75 323.9 11.25 285.8 12.00 304.8
12 13.50 342.9 15.00 381.0 13.00 330.2 15.00 381.0 13.50 342.9 15.00 381.0 13.50 342.9 14.25 362.0
14 14.75 374.6 16.25 412.8 ----14.75 374.6 16.25 412.8 14.75 374.6 15.50 393.7
16 16.75 425.4 18.50 469.9 ----16.75 425.4 18.50 469.9 16.75 425.4 17.62 447.5
18 19.25 489.0 21.00 533.4 ----19.25 489.0 21.00 533.4 19.25 489.0 20.12 511.2
20 21.00 533.4 23.00 584.2 ----21.00 533.4 23.00 584.2 21.00 533.4 22.00 558.8
24 25.25 641.4 27.25 692.2 ----25.25 641.4 27.25 692.2 25.25 641.4 26.25 666.8
INCHES MM
INCHES MM INCHES MM
INCHES MM
INCHES MM
INCHES MM
INCHES MM
INCHES MM
Style R-4 gaskets may be compressed an
additional amount when exposed to the higher
bolt loads, but not to the degree that the gasket
will be crushed due to the radial support
provided by the confining groove.
Special Style R gaskets are adaptable to
non-standard flanges and can be designed
and manufactured according to specifications
for high and low pressure applications and for
severe corrosive conditions.
When ordering special Style R gaskets for
non-standard flanges and for special
applications,contact the Applications
Engineering Team.