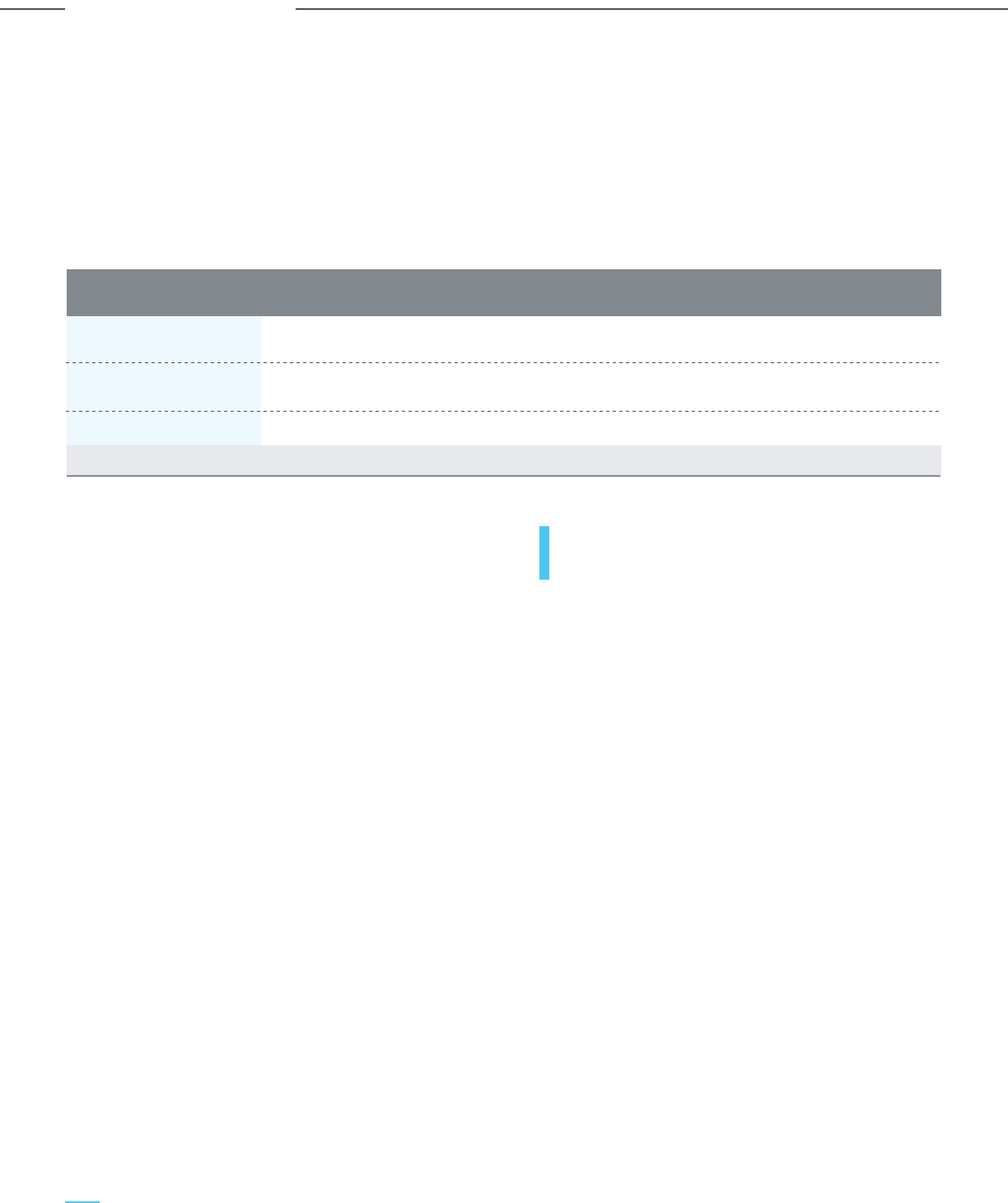
Table 5-5: Sedimentary Basins Spanning Across Multiple Regions
Basin name Basin category State/UT Theoretical storage potential
(Gt of CO
2
)
Vindhyan Category II Madhya Pradesh/ 11.81
Uttar Pradesh/ Rajasthan
Satpura- Category III Madhya Pradesh/ 1.87
South Rewa- Damodar Chhattisgarh/Jharkhand
Bhima-Kaladagi Category III Maharashtra/ Karnataka 0.41
Total 14.09
ECBMR: The potential for ECBMR is localized in the
eastern region due to the presence of major
coalfields. These can be storage clusters for
industries that are close to the coalfields, such as
steel and power plants.
EOR: The potential for EOR will increase in the future
as more wells are maturing and newer wells may be
discovered through exploratory activities.
Storage in basalt formations: Mineralization in
basalt formations provides a large opportunity for
CO
2
storage in the western region, but is currently in a
nascent stage of development.
Comparing the region-wise emission volumes during
the time horizon of 2030 – 2050 and the theoretical
storage capacity, sufficient storage capacity is
available for cluster formation in each region. The
formation of hubs will result in a smooth transfer of
CO
2
between clusters of different regions. Apart from
the four CO
2
disposition options discussed above,
several other CO
2
utilization clusters (CO
2
to
chemicals, new utilization techniques, etc.) can evolve
and become more viable over time, thus increasing
the options for abatement of enhanced volumes of
CO
2
from the power and industrial sector.
5.6 Key Risks Associated
with CCUS
The CCUS policy framework for India should also
address the key risks associated with the CCUS value
chain. CCUS projects integrate various sub-systems
such as carbon capture, transportation, and
sequestration. The interfaces between the
sub-systems projects involve complex interfaces and
lead to risks associated with CCUS projects. Some of
the key risks and their mitigation measures are
described below:
5.6.1 Technical Risks
5.6.1.1 Reservoir Suitability for CO
2
Flooding
for EOR
The extent of CO
2
abatement possible through EOR
depends on the comparative performance and
cost-effectiveness of CO
2
EOR vis-à-vis other methods
of tertiary recovery like nitrogen injection, polymer
injection, steam injection, natural gas injection, and
the use of foaming agents. Some of the current
developments, such as the use of foams or other
chemicals to improve sweep efficiency may reduce the
attractiveness of CO
2
EOR, while on the other hand,
The region-wise storage cluster formation shows that
sequestration in deep saline aquifers has the best
potential in all the regions. Due to the lack of data on
the northern sedimentary basins, the theoretical
storage capacity for saline aquifers is low. But as more
exploratory activities are carried focused on CO
2
storage, the storage potential in the northern region is
likely to increase. Few sedimentary basins span across
multiple states and they have been mentioned in
Table 5-5.
exploration and production from more complex
hydrocarbon resources may increase the role of CO
2
.
Hence it is necessary to monitor the developments of
other tertiary recovery systems, as well as use
improved reservoir simulation tools to understand
CO
2
flooding and EOR performance. It is also
important to calibrate financial commitments to
capacity expansions based on assured future offtakes
for CO
2
to mitigate this risk.
5.6.1.2 Change in Processes Emitting Industries:
This risk emanates from the possibility of using
electricity or new clean energy carriers to replace the
use of fossil fuels in industrial processes like iron &
steel or cement, thereby substantially impacting the
CO
2
emissions available for capture. Even the power
sector is not immune to such changes: for example,
base-load plants may transition to only peaking
operations, limiting the quantity of CO
2
emissions.
Therefore it is important to develop a understanding
of the industrial processes and the likely trajectory of
technological innovation in the industry, as well as the
risk of the end-products of the industry getting
replaced by alternate products.
5.6.1.3 Offshore Unloading & Condition of
Shipped CO
2
CO
2
shipping is considered a future alternative to CO
2
piping and would involve vessels similar to
semi-refrigerated LNG/LPG carriers that use
pressurized tanks. Compared to a fixed pipeline based
distribution network, CO
2
shipping provides flexibility
to adjust to demand-supply dynamics and deploy
ships/barges to different consumption points and
allows for more gradual expansion of the CCUS
system. One key issue is converting liquid CO
2
from
temperatures as low as -50°C to a temperature
suitable for injection. Significant heat energy would be
required, involving cost and emissions, if done with
fossil fuels. The logistics of ship unloading also need
to be addressed, including issues related to ship
loading & unloading rates to limit demurrage as well
as using floating barges for offshore offloading.
5.6.1.4 CO
2
Specification Challenges
Most carbon capture solutions try to address and
meet the required CO
2
specifications. The key
requirement is adequate dehydration, along with
other impurity tolerances depending on the CO
2
source and capture process. However, problems may
arise when integrating multiple CO
2
sources and
capture processes, and additional treatment of the
captured raw CO
2
may be required, depending on the
disposition pathway for the CO
2
. These requirements
would depend on the diversity of CO
2
sources in a
particular cluster, which increases the likelihood of
CO
2
mixing issues. The other issues to be handled are
the concentration of non-condensable and inert
impurities such as nitrogen and argon, that have an
effect on pipeline and reservoir capacity.
5.6.2 Financial Risks
5.6.2.1 Cost of Capture
The main cost driver in the CCUS value chain is the
capture cost. In industrial processes such as natural
gas processing and gasification, carbon capture is part
of the process itself and hence there is no additional
cost of carbon capture. However, in the case of thermal
power plants and other industrial processes, there are
significant capital and cash costs, leading to financial
risks for the entire CCUS value chain, which need to be
mitigated through suitable commercial arrangements.
Significant resources have been invested in developing
more efficient and cost-effective carbon capture
technologies, and the cost range for most
commercial-scale carbon capture technologies is well
established. It may be worthwhile to focus further R&D
efforts on finding creative ways to sell or consume the
CO
2
product in new ways or optimize opex through
low-cost sources of low-grade heat/steam for solvent
regeneration and meet the electricity duty
requirements of other carbon capture technologies.
5.6.2.2 Financing Risks
The CCUS value chain consists of several connected
sub-systems and functions that must act in
coordination for the overall success of the project.
Multiple sources or sinks in a cluster mitigate the risk
and may require more elaborate transport and storage
infrastructure, leading to higher capital costs and
financing requirements, particularly in the early
“anchor” stages of the project. The risk of financing
delays or inadequacy leads to cost escalation and
hence needs to be mitigated through measures such as
meticulous planning, access to bridge financing during
the early stage of the project and making realistic
provisions for additional funding to cover the
contingency of delays.
5.6.2.3 Loss of Storage Site
Complications during CO
2
injection may lead to the
stoppage of operations at CO
2
storage sites. Although
reservoir management should provide adequate warning
of such occurrences, there are technical risks in
estimating/predicting the final capacity of a new storage
site with certainty. Relying on a single site or a single
well is a key technical risk. Hence there is a need to
prove new storage sites to ensure continued operations.
Careful long-term planning and contracting of multiple
sites can mitigate this risk. Drilling additional wells or
temporarily increasing the injectivity of existing wells
can boost the short-term capacity of alternate sites.
Hence, it is recommended that contingency plans be
developed for additional storage capacity via additional
wells or reservoirs. If rigs and requisite well supplies
are available, new wells can be drilled and completed
fast. It is therefore prudent to ensure rapid access to
drilling rather than storing spare wells, as well as
developing and assessing multiple storage locations.
5.6.2.4 Price of Green Products
The issue of “inadequate prices” for low carbon or
green products is a major risk factor. To address this
risk, renewable energy has widely used feed-in tariffs,
but only until it became cost-competitive. The tariff is
paid centrally and passed on to consumers via taxation
or a general price increase. However, the system is
inflexible as the pre-determined feed-in tariff rates may
become inappropriate and may need to be lowered.
Ultimately the higher costs for the commitment for
green products has to be passed on to customers and
businesses, since the Government’s revenues comes
from citizens and businesses.
5.6.2.5 Lack of Tradeable Long Term CO
2
Emission
Reduction
CCUS ensures long-term emission reductions and
requires long term investments and financing having
time horizons of up to 40 years. There is a need to
design financial instruments where the payoffs/rewards
are directly related to CO
2
abatement levels. The
probable investors/buyers would be organizations that
need to achieve future carbon reductions. The potential
to invest directly in the best CCUS locations/projects
should be less expensive than purchasing abatement
certificates. There is thus a need to structure financial
products directly linked to specific CO
2
abatement,
transportation, and storage quantities, which can be
marketed to different types of investors (viz.
individuals, institutions and industrial enterprises), and
preferably in a globally tradable manner.
5.6.2.6 Withdrawal of Key Partners & Delay
The CCUS value chain requires the interplay and
association of multiple partners and the
withdrawal/loss of a partner in the value chain can
compromise the entire system. Contracts need to be
designed to prevent the same, as well as protect the
project from changes in ownership or divestments.
However, there is the residual risk of a business
partner’s insolvency or business failure. One model
could be to centralize the core activities related to the
CCUS value chain within one dedicated well-funded
organization (with a lower probability of failure or
disruption) rather than having multiple partner
organizations and procuring the balance support
services from the market.
5.6.3 Safety Risks
5.6.3.1 Pipeline Incidents
Pipeline related accidents and incidents are significant
safety risks and need to be mitigated through adequate
insurance to cover the costs of paying compensation to
affected parties and the cost of repairing the pipeline.
Permanent disruption or permanent stoppage of CO
2
transportation may occur if the entire CCUS
facility/infrastructure has been destroyed.
The effect of one pipeline incident may spill over to the
development of the CCUS industry and operations of
already commissioned CCUS facilities, who would need
to upgrade their operations and safety protocols.
Fortunately, there have been no major failures or
disasters to date in the CCUS industry. At the same
time, it is necessary for strict international safety
standards to be adopted to preemptively avoid any
incident. The safety standards followed in the
international seaborne movement of LNG provides an
excellent example worth emulating.
5.6.3.2 Large Dia Pipeline in Populated Areas
Historical pipeline incident records reveal that larger
diameter lines generally have a lower frequency of
incidents. In order to avoid any incidents, automatic
isolation valves at short intervals and leak monitoring
systems are two solutions adopted by some projects.
CO
2
is not dangerous in moderate quantities and
becomes life-threatening only above certain
threshold levels. However, adequate safety and
failsafe precautions need to be adopted for dense
phase or supercritical CO
2
pipeline transport in
populated areas, as may be required for developing
large scale CCUS projects in densely populated
countries like India, along with clearly defined and
established emergency response and communication
protocols.
132
Carbon Capture Utilization and Storage (CCUS) –
Policy Framework and Deployment Mechanism in India
Carbon Capture Utilization and Storage (CCUS) –
Policy Framework and Deployment Mechanism in India
CCUS Policy Framework for India