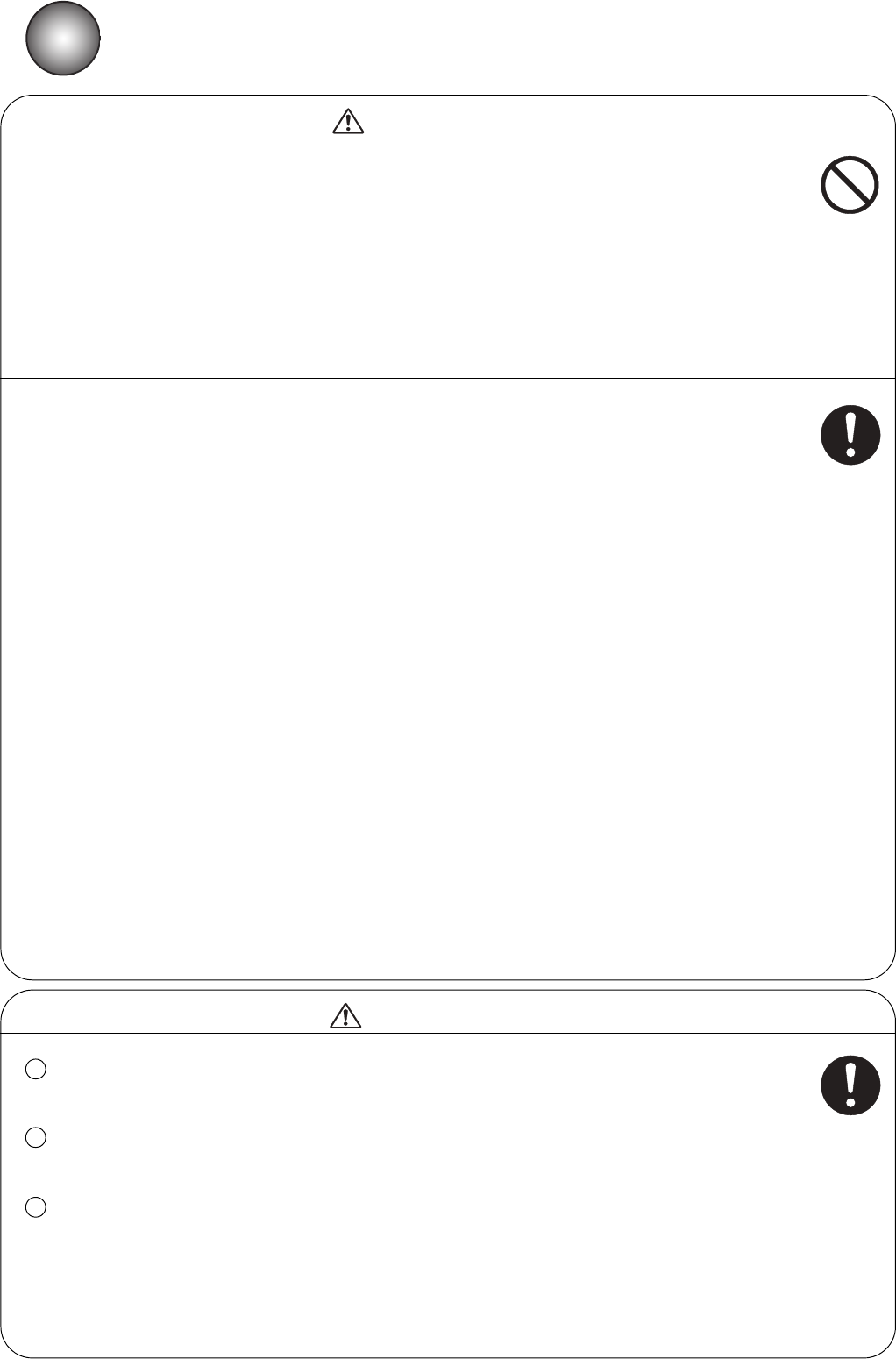
6-1 ●Circulation System Work and Adjustment Method
● When replenishing the ink and makeup, changing the ink, or performing other work in
which the ink and makeup are handled, be sure not to spill the ink and makeup.
If the ink and makeup is accidentally spilled, quickly wipe it off with wiping paper, etc.
Do not close the maintenance cover until you verify that the wiped parts are
completely dry.
Since the ink and makeup vapor will collect inside the printer especially in the state in
which the ink and makeup was spilled inside the printer and was not wiped off
completely, it will cause ignition and fire.
When wiping is difficult in the energized state, perform shutdown processing with the
maintenance cover remaining open and turn off the power, then perform wiping
again.
● If leaking of the ink and makeup inside the printer was detected during printer
operation or maintenance, quickly wipe it with wiping paper, etc. and perform
shutdown processing with the maintenance cover remaining open and turn off the
power, then repair the leak.
If operation is continued when the ink and makeup is leaking, it will cause trouble
and prevent normal printing will become.
In addition, since the ink and makeup are combustible, they may cause a fire.
● The ink and makeup, their waste solution, used wiping papers and empty containers
are flammable. Waste disposal must comply with appropriate regulations.
Consult the appropriate regulatory agency for further information.
● When the ink particles are caught in a beaker during test printing, etc., use a
conductive beaker and securely connect the beaker to a ground.
In addition, be sure that the print head is not inserted into the beaker.
Since the ink particles used in printing are electrically charged, if the beaker is not
connected to a ground, the charge load will gradually increase and cause a fire.
6. CIRCULATION SYSTEM WORK
AND ADJUSTMENT METHOD
● Never pour the ink and makeup waste into a sewer, etc.
Have the ink and makeup drainage processed by an industrial waste processor as
special control industrial waste and used wiping papers and the empty container as
industrial waste.
● Do not remove, apply unreasonable force to, or bend the piping tubes unnecessarily.
Since high pressure is applied to parts of the ink and solvent inside the piping tube,
the ink and solvent may spurt out and get into your eyes and mouth or soil your
hands and clothing.
If the ink or solvent gets into your eyes or mouth, immediately rinse it out with warm
water and see a doctor.
WARNING
● Pay careful attention to the following items regarding handling of the ink and makeup:
Wear gloves and goggles so that the ink and makeup will not directly contact your
skin.
If the ink or makeup gets on your skin, wash it off with soap and warm water.
When taking the bottle from the printer, be careful that the ink does not get on the
printer or surroundings. If the ink or makeup gets on the equipment or
surroundings, immediately wipe it off with makeup.
Since the vapor pressure of the makeup is generally high, if the ambient
temperature is high such as in the summer, etc., the internal pressure will rise and
makeup could spurt out when the outside cover is removed. Therefore, when
unplugging,
●do not hold the bottle near your face
●place the can on a level surface
●open while covering the opening with a rag, etc.
CAUTION
1
2
3