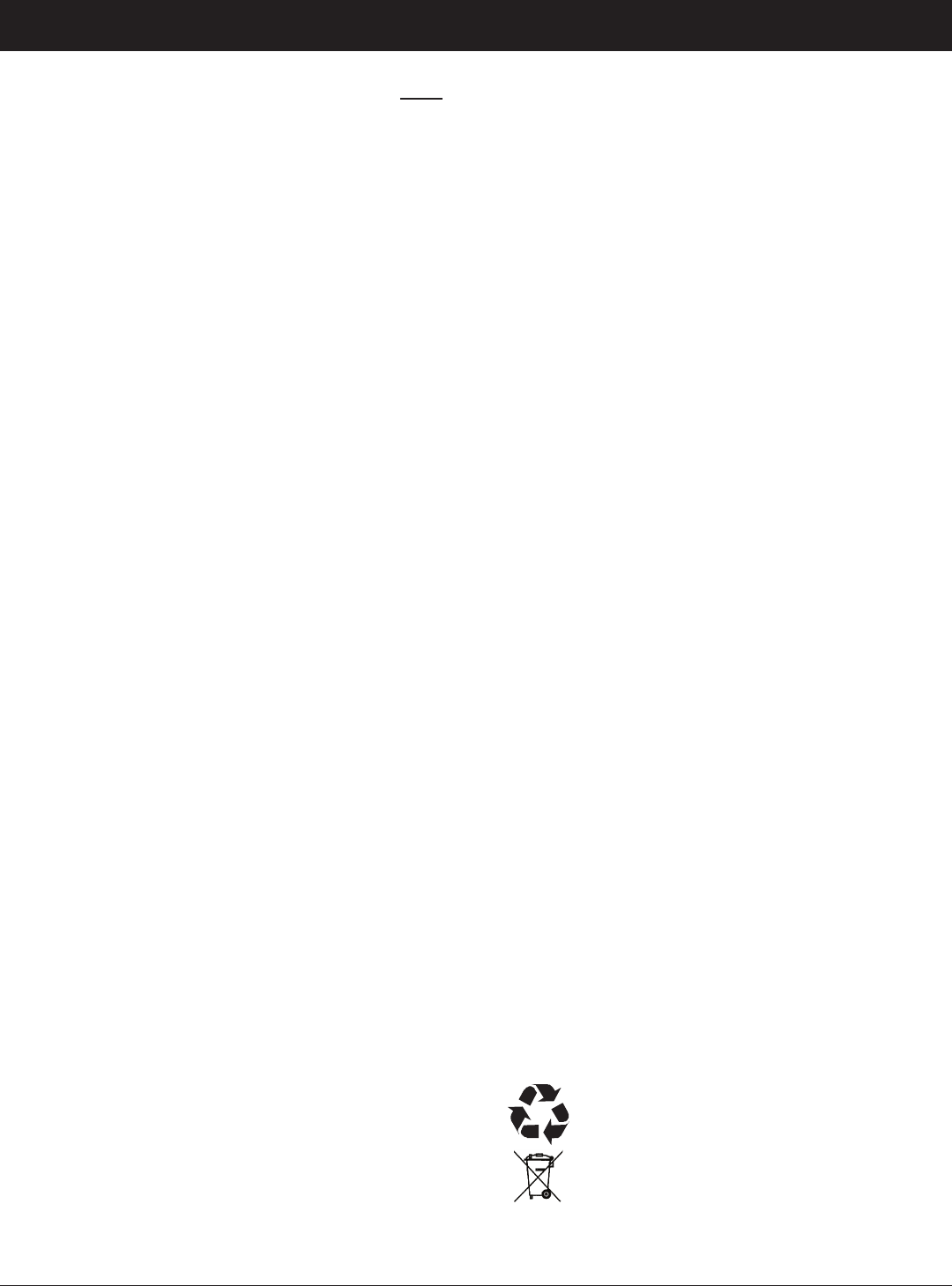
2
ECOWATER
S Y S T E M S
Table of Contents & Safety Guides
that is in a dry location only, grounded and properly
protected by an overcurrent device such as circuit
breaker or fuse.
This system is not intended to be used for treating water
that is microbiologically unsafe or of unknown quality
without adequate disinfection before or after the system.
FCC NOTICE
NOTE: This equipment has been tested and found to
comply with the limits for a Class B digital device, pur-
suant to Part 15 of the FCC Rules. These limits are
designed to provide reasonable protection against
harmful interference in a residential installation. This
equipment generates, uses, and can radiate radio fre-
quency energy and, if not installed and used in accor-
dance with the instructions may cause harmful interfer-
ence to radio communications. However, there is no
guarantee that interference will not occur in a particular
installation. If this equipment does cause harmful inter-
ference to radio or television reception, which can be
determined by turning the equipment off and on, the
user is encouraged to try to correct the interference by
one or more of the following measures:
= Reorient or relocate the receiving antenna.
= Increase the separation between the equipment and
receiver.
= Connect the equipment into an outlet on a circuit dif-
ferent from that to which the receiver is connected.
= Consult the dealer or an experienced radio/TV tech-
nician for help.
Changes or modifications not expressly approved by
EcoWater Systems could void the user’s authority to
operate the equipment.
This device complies with Industry Canada Standard
RSS-210. Operation is subject to the following two con-
ditions: (1) this device may not cause interference, and
(2) this device must accept any interference, including
interference that may cause undesired operation of the
device.
Ce dispositif est conforme avec la norme CNR-210
d’Industrie Canada. Le fonctionnement du dispositif
est sujet aux deux conditions suivantes: (1) le dispositif
ne doit pas causer de brouillage, et (2) le dispositif doit
accepter tous brouillages, incluant tous brouillages qui
peut nuire au bon fonctionnement du dispositif.
European Directive 2002/96/EC requires all
electrical and electronic equipment to be dis-
posed of according to Waste Electrical and
Electronic Equipment (WEEE) requirements.
This directive or similar laws are in place
nationally and can vary from region to region.
Please refer to your state and local laws for
proper disposal of the equipment.
SAFETY GUIDES
Follow the installation instructions carefully. Failure to
install the water filtration system properly voids the
warranty.
Before you begin installation, read this entire manual.
Then, obtain all the materials and tools you will need to
make the installation.
Check local plumbing and electrical codes. The
installation must conform to them.
Use only lead-free solder and flux for all sweat-solder
connections, as required by state and federal codes.
Use care when handling the water filtration system. Do
not turn upside down, drop, or set on sharp protrusions.
Do not locate the water filtration system where freezing
temperatures occur. Do not attempt to treat water over
120°F. Freezing, or hot water damage voids the
warranty.
Avoid installing in direct sunlight. Excessive sun heat
may cause distortion or other damage to non-metallic
parts.
The water filtration system requires a minimum water
pressure of 30 psi at the inlet. Maximum allowable
inlet water pressure is 125 psi. If daytime pressure is
over 80 psi, nighttime pressure may exceed the maxi-
mum. Use a pressure reducing valve if necessary
(Adding a pressure reducing valve may reduce the flow).
The water filtration system works on 24V DC electrical
power, supplied by a direct plug-in power supply
(included). Be sure to use the included power supply,
and plug it into a nominal 120V, 60 Hz household outlet
TABLE OF CONTENTS Page
Specifications & Dimensions . . . . . . . . . . . . . . . . . . . 3
Before Starting Installation . . . . . . . . . . . . . . . . . . . . 4
Media Loading . . . . . . . . . . . . . . . . . . . . . . . . . . . . . . 5
Typical Installation Illustrations . . . . . . . . . . . . . . . . . 6
Installation . . . . . . . . . . . . . . . . . . . . . . . . . . . . . . . 7-8
General Information . . . . . . . . . . . . . . . . . . . . . . . . . 9
Sanitizing Procedure . . . . . . . . . . . . . . . . . . . . . . . . . 9
Setup Procedure . . . . . . . . . . . . . . . . . . . . . . . . 10-13
Filter Operation . . . . . . . . . . . . . . . . . . . . . . . . . . 14-25
Service Information . . . . . . . . . . . . . . . . . . . . . . 26-31
Troubleshooting Guide . . . . . . . . . . . . . . . . . . . . . . 28
Wiring Schematic . . . . . . . . . . . . . . . . . . . . . . . . . . . 28
Repair Parts . . . . . . . . . . . . . . . . . . . . . . . . . . . . 33-35
Warranty . . . . . . . . . . . . . . . . . . . . . . . . . . . . . . . . . 36