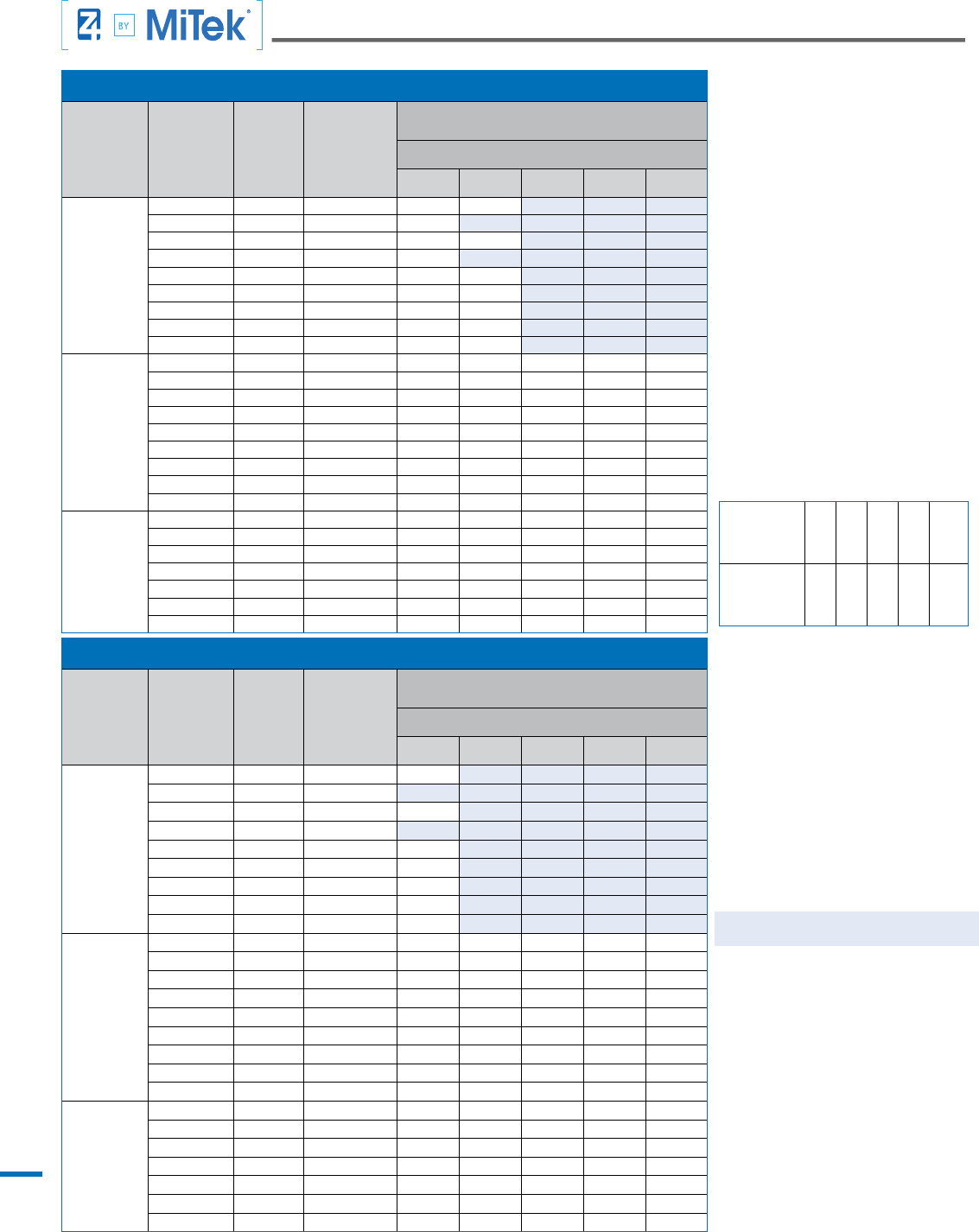
16
Notes
1. Wood compression members are not a Z4
product and are not provided with Z4 Tie-Down
Systems.
2. All values assume single species installation.
The Engineer of Record is responsible for designs
with more than one species or for heights not listed
in these tables.
3. Wall depth (b) = 3.5 inches for nominal 4-inch,
5.5 inches for nominal 6-inch, and 7.25 inches for
nominal 8-inch wall depths
4. Maximum design compression capacities
perpendicular to grain, Pc are based on wood
compressive strengths equal to 625 psi for DF-L,
405 psi for HF, 425 psi for SPF, and 565 psi for SP.
5. The Bearing Area factor, C
b
, is not included
in table values. For bearing areas located 3” or
more from the end of the horizontal member,
perpendicular to grain capacities, P
c⊥
, may be
multiplied by the following factor:
6. Maximum design compression capacities
parallel to grain, P
c
are based on the tabulated
wood species, effective length, cross-sectional
area, and grade in compliance with the 2015
National Design Specication (NDS).
7. Loads shown are for axial compression of
individual single member capacities. Individual
capacities may be combined when multiple
members are installed, stitch nailing not
required.
8. Parallel to grain capacities P
c
include a load
duration factor, C
D
. Increase equal to 1.60.
9. Shaded cells represent capacities governed by
compression parallel to grain.
10. The lumber effective length (le) for an 8-ft
nominal wall height is equal to 92-1/4" for DF-L
and 92-5/8" for HF, SPF, and SP. l
e
/ b ≤ 50.
TABLE 2.1- SP: COMPRESSION CAPACITIES FOR SOUTHERN PINE
1, 2
Nominal Wall
Depth, b
3
(in)
Nominal
Lumber
Dimensions
Lumber
Grade
P
c⊥
Maximum
Compression
Capacity
Perpendicular to
Grain (lbs.)
4, 5
P
c
- Maximum Design Compression Capacity Parallel to
Grain (lbs.)
6, 7, 8, 9
Nominal Wall Height (ft.)
10
8 9 10 11 12
4"
2x4 No. 2 2,965 2,980 2,365 1,920 1,590 1,335
2x4 Stud 2,965 2,615 2,105 1,725 1,435 1,210
3x4 No. 2 4,945 4,970 3,945 3,200 2,650 2,225
3x4 Stud 4,945 4,360 3,510 2,875 2,390 2,015
4x4 No. 1 6,920 7,910 6,280 5,100 4,215 3,545
4x6 No. 1 10,875 12,345 9,820 7,980 6,605 5,555
4x8 No. 1 14,335 16,180 12,890 10,485 8,685 7,305
4x10 No. 1 18,290 20,500 16,360 13,325 11,050 9,300
4x12 No. 1 22,245 24,855 19,855 16,180 13,420 11,295
6"
2x6 No. 2 4,660 10,165 8,380 6,965 5,850 4,970
2x6 Stud 4,660 7,520 6,605 5,730 4,955 4,290
3x6 No. 2 7,770 16,940 13,970 11,610 9,750 8,280
3x6 Stud 7,770 12,530 11,005 9,550 8,255 7,150
6x4 No. 1 10,875 26,450 21,945 18,305 15,410 13,110
6x6 No. 1 17,090 30,025 26,820 23,595 20,610 17,975
6x8 No. 1 23,305 40,940 36,575 32,180 28,105 24,515
6x10 No. 1 29,520 51,860 46,325 40,760 35,595 31,050
6x12 No. 1 35,735 62,775 56,080 49,340 43,090 37,585
8"
2x8 No. 2 6,355 19,750 17,540 15,355 13,365 11,625
3x8 No. 2 10,595 32,915 29,235 25,595 22,270 19,375
4x8 No. 1 14,830 50,260 45,060 39,770 34,815 30,420
6x8 No. 1 23,305 48,185 45,970 43,335 40,340 37,130
8x8 No. 1 31,780 65,705 62,690 59,095 55,010 50,630
8x10 No. 1 40,255 83,225 79,405 74,850 69,680 64,130
8x12 No. 1 48,730 100,745 96,125 90,610 84,345 77,635
TABLE 2.1- SPF: COMPRESSION CAPACITIES FOR SPRUCE-PINE-FIR
1, 2
Nominal Wall
Depth, b
3
(in)
Nominal
Lumber
Dimensions
Lumber
Grade
P
c⊥
Maximum
Compression
Capacity
Perpendicular to
Grain (lbs.)
4, 5
P
c
- Maximum Design Compression Capacity Parallel to
Grain (lbs.)
6, 7, 8, 9
Nominal Wall Height (ft.)
10
8 9 10 11 12
4"
2x4 No. 2 2,230 2,930 2,340 1,905 1,575 1,325
2x4 Stud 2,230 2,415 1,955 1,605 1,335 1,130
3x4 No. 2 3,720 4,885 3,895 3,175 2,630 2,210
3x4 Stud 3,720 4,030 3,255 2,670 2,225 1,880
4x4 No. 1 5,205 6,840 5,455 4,440 3,680 3,095
4x6 No. 1 8,180 10,710 8,550 6,965 5,775 4,860
4x8 No. 1 10,785 14,060 11,235 9,160 7,600 6,400
4x10 No. 1 13,760 17,850 14,285 11,655 9,675 8,150
4x12 No. 1 16,735 21,710 17,375 14,175 11,765 9,910
6"
2x6 No. 2 3,505 9,600 8,055 6,770 5,725 4,885
2x6 Stud 3,505 6,915 6,100 5,310 4,605 3,995
3x6 No. 2 5,845 16,000 13,425 11,280 9,545 8,145
3x6 Stud 5,845 11,525 10,165 8,850 7,670 6,655
6x4 No. 1 8,180 22,040 18,585 15,665 13,280 11,350
6x6 No. 1 12,855 25,545 22,840 20,115 17,580 15,340
6x8 No. 1 17,530 34,835 31,150 27,430 23,970 20,915
6x10 No. 1 22,205 44,125 39,455 34,740 30,360 26,495
6x12 No. 1 26,880 53,415 47,760 42,055 36,755 32,075
8"
2x8 No. 2 4,780 17,875 16,215 14,465 12,770 11,230
3x8 No. 2 7,970 29,790 27,025 24,110 21,285 18,715
4x8 No. 1 11,155 40,420 36,880 33,090 29,350 25,895
6x8 No. 1 17,530 40,930 39,070 36,850 34,330 31,620
8x8 No. 1 23,905 55,810 53,280 50,255 46,810 43,115
8x10 No. 1 30,280 70,695 67,485 63,655 59,295 54,615
8x12 No. 1 36,655 85,580 81,695 77,055 71,780 66,110
Thickness
of Horizontal
Member (in)
1.5 2.5 3.5 5.5 ≥ 6.0
C
b
Factor 1.25 1.15 1.11 1.07 1.00
Wood Compression Post Capacities